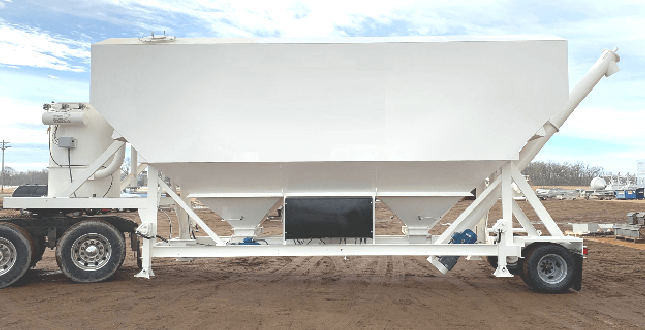
Low Profile Cement Silos
Portable Low Profile Cement Silos
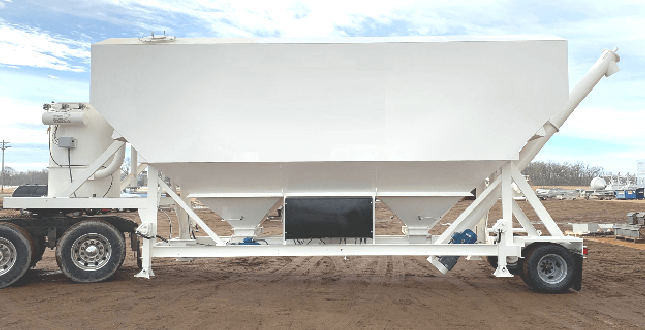
300 Bbl Low Profile Portable Cement Silo
8’-6” Wide x 34’-3” Overall Length • Positive Feed Auger System • 7″ Diameter Carry Across and 9″ Diameter Discharge Screw x 17′-0″ • 10 HP Motor and Gear Box Drive • Heavy Duty Axle Trailer and Tires • Electric Brakes and Lights Package • 330 Ft.² Pulse Jet Dust Collector with Cartridge-Type Filters • Solimar Vibratory Disc Aeration • Pressure Relief Valve • High and Low Bin Level Indicators with Lighted Alarms • 4″ Fill Pipe with Aluminum Adapter • (4) Two-Speed Trailer Jacks • 20″ Non-Pressurized Inspection Manhole • Sand Blast, Prime, and Paint – White, Gray, Tan, or Yellow
Options: Upgrade to 9″ Carry Across and 12″ Discharge Screw Conveyor • Single Phase Motor or Hydraulic Drive Motor • Motor Starter Controls • Manual Air Valve Controls • Air Brakes and Lights Package
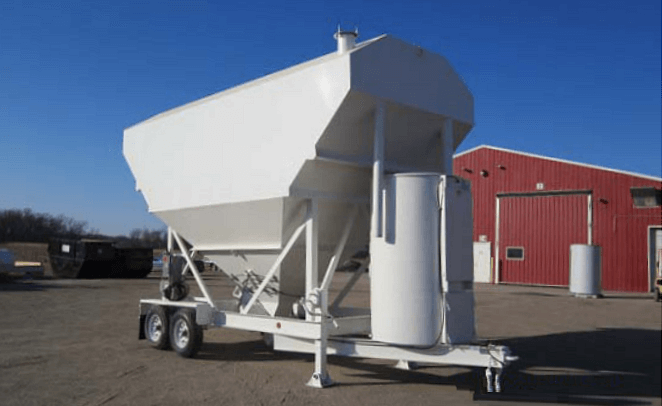
200 Bbl Low Profile Portable Cement Silo
8’-6” Wide x 25-9” Overall Length • Positive Feed Drive Auger System • 7″ Diameter Screw x 17′-0″ • 5 HP Motor and Gear Box Drive • Heavy Duty Axle Trailer and Tires • Electric Lights and Brakes Package • 330 Ft.² Pulse Jet Dust Collector with Cartridge-Type Filters • Solimar Vibratory Disc Aeration • Pressure Relief Valve • High and Low Level Indicators with Lighted Alarms • 4″ Fill Pipe with Aluminum Adapter • (4) Two-Speed Trailer Jacks • 20″ Non-Pressurized Inspection Manhole • Sand Blast, Prime, and Paint – White, Gray, Tan, or Yellow
Options: Upgrade to 9″ Screw Conveyor • Single Phase Motor, Hydraulic Drive Motor, or 16 HP Gas Motor • Motor Starter Controls • Manual Air Valve Controls